What is a Cold Plate for thermal management?
Cold plate (also called cooling plates or liquid cold plate) is a metallic plate with a fluid circulating inside. The fluid will drain the heat from the components mounted on the cold plate, outside of the system.
The thermal transfer is forced by a liquid circulating in the metal sheet (Mainly aluminium, might be copper) at medium to low pressure.
Cold plates are used for thermal management, particularly in high-performance computing and power electronics applications. Cold plates are used when heat transfer by air is not sufficient.
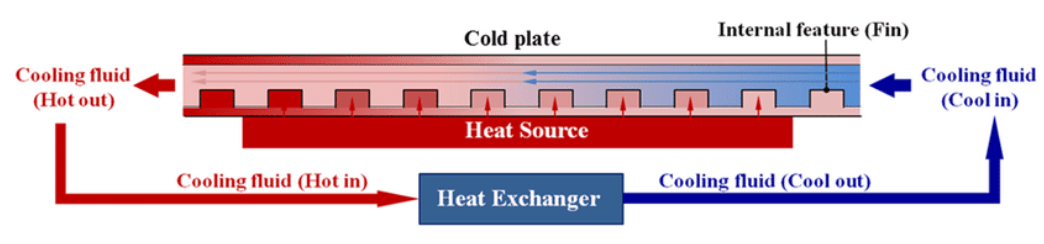
As electronic components are more and more powerful and space are limited with miniaturization: the density and quantity of heat to dissipate in electronic projects is continuously increasing. The cold plates are an impactful solution for thermal management thanks to the high customization possibilities and the capacity to dissipate high quantity of heat in small spaces.
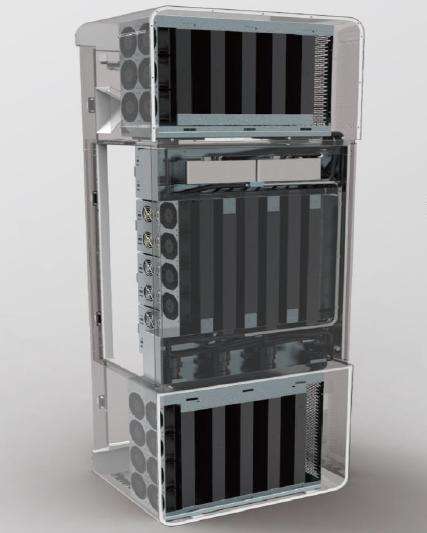
What are the main field of application for cold plates?
The cold plates are widely used for battery cooling (especially for electrical vehicle application), data center cooling, laser or medical equipment cooling, as well as in industry field.
Our actual distribution is: Industry: 35%, Medical: 20%, Telecom: 20%, Energy: 15%, Automotive:10%.
Automotive field is growing due to electrification of new vehicles (EV).
What cold plate are made for?
Heat transfer by air is limited. To dissipate large amounts of power by air, a large mass flow rate is required (because heat transfer capacity is limited by the density of the fluid).
25 < hair< 250 W/m2.K
100 < hliquid< 20 000 W/m2.K
As liquid is denser than air: Liquid cooling is able to achieve better heat transfer at much lower mass flow rates.
That is why a liquid cooled system is generally used in cases were large heat loads or high-power densities need to be dissipated and air would require a very large flow rate.
Temperature range requirements defines the type of liquid that can be used in each application.
− Operating Temperature < 0°C, then water cannot be used.
− Glycol/water mixtures are commonly used in military applications, but the heat transfer capabilities are significantly lower than water only.
How is a cold plate used?
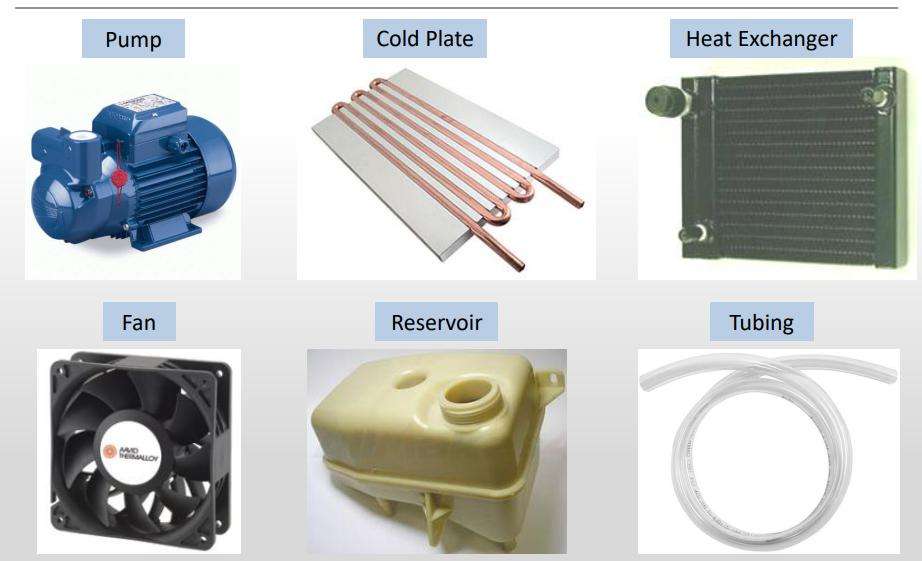
A cold plate is made from a metal plate with high thermal conductivity (such as aluminium or copper) that is in direct contact with hot components. The cold plate is designed to have a high surface area to increase heat transfer. The heating components are mounted directly on the cold plate for an efficient thermal transfer. The heat is drain out of the cold plate thanks to a fluid circulating through the cold plate. Then the fluid is cooled outside of the cold plate thanks to a heat exchanger.
The cold plates are a part of a global management system composed of:
– Pump for the fluid: the pump needs to be dimensioned following the global thermal management system (size of the cold plate, heat to dissipate, kind of fluid used, etc).
– Fan and heat exchanger plate: this part of the system is required to cool down the fluid heated in the cold plate. The fluid is circulating through the heat exchanger plate, and cooled by air transfer force by a fan.
– Tubing: used to connect the pump to the cold plate and to the heat exchanger and compression tank.
– Decompression tank: as the fluid temperature changes, the volume changes too. That is why a decompression tank is required. It will avoid over-pressure in the thermal management system.
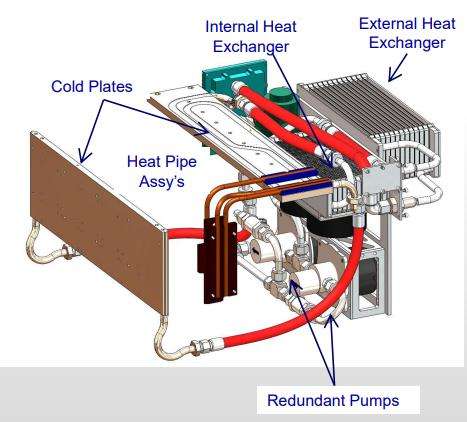
The cold plate can also be assembled in an opened thermal management system. In that case,the cooling fluid used will not be reused (only possible with water).
What are the characteristics of a cold plate?
Compacity and assembly:
Cold plates are really efficient especially when heat power to dissipate is dense. The manufacturing process, from a metallic plate, permits a high compactness and to the components to be mounted directly on the cold plate. The cold plate can then be used as a key structure for the electronic system. The connection between the cold plate and the rest of the system is mainly done using pluggable connectors (as G1/8) screwed on a dedicated brass connector machined on the cold plate.
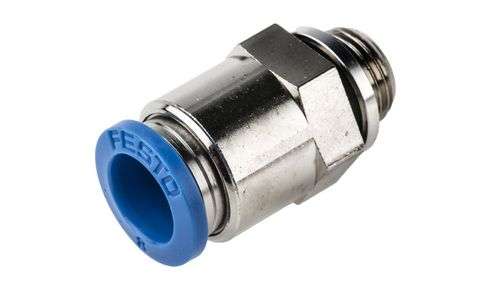
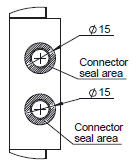
Power and operating range:
The capacity to dissipate the power depends on the design of the cold plate and the material used. However, a standard design can dissipate tens of kilo Watt. Depending on the fluid used, the operating temperature can be from -25°C to +150°C. Cold plates are mainly used with water. In that case operating temperature would be closer to 5°C up to 90°C, due to the fluid characteristics of the water.
What are cold plates made of?
Material of the cold plate:
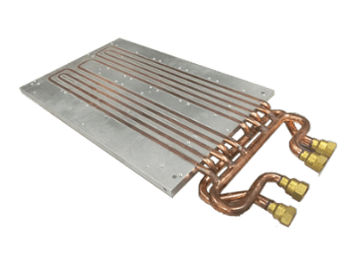
The main material used for cold plate is aluminium (AL6061 or AL6063) because it has good thermal conductivity, it is easy to manufacture and raw material price is lower than copper. For specific parts of the cold plate, we can use copper for its high thermal conductivity properties, especially for tubes.
The connectors of the cold plates are mainly made with brass, because it is easy to CNC machine and to braze.
Surface treatment (total or partial) can also be made (for example Surtec 650, or anodizing).
Other material as EPDM, silicone or polyurethane foam, can be used for electric insulation or IP(fluids or particles) sealing on a cold plate.
Cooling fluids used:
The main fluid used in cold plates is water (or glycol/water). Indeed, water provides superior cooling performances in a cold plate. On the other hand, because of freezing temperature around 0°C and boiling point around 100°C, this fluid might limit the operating temperature range of the cold plate.
That is why it can be mixed with glycol to reduce freezing risks and increase thermal performance.
Other fluids can be used, but some might provide lower thermal performance in a cold plate. The compatibility with the material used for the cold plate or the tubes is also to keep in mind to avoid any corrosion risk.
You can find below the compatibility between the different cold plate materials and the fluids.
How is a cold plate manufactured?
There is 3 ways to manufacture a cold plate:
Copper tube laminated on an aluminium plate (with epoxy resin for junction).
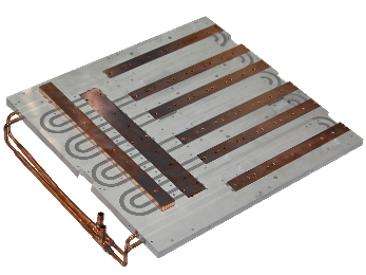
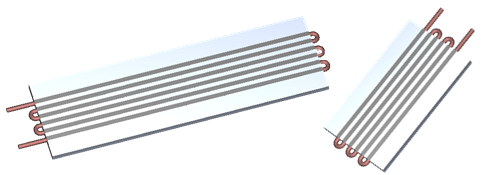
Firstly, the aluminium plate is CNC machined following the path of the fluid and the required fixation and operations specified. On the same time the tube is pre-formed (mainly copper tube, but could be aluminium tube or stainless steel).Then the cold plate is covered with epoxy resin to prepare the tube lamination. The tube is then laminated on the cold plate, chasing the epoxy resin. The remaining epoxy resin ensures a complete physical contact between the machined cold plate and the laminated tube.
The final cold plate is then surfaced to ensure the right flatness and remove surplus of epoxy resin.The tubes can crop out at the surface or be covered by a layer of epoxy resin to be totally buried.
The tubes laminated on the cold plate can also be Aluminium or Stainless Steel (even if thermal conductivity is lower, price is also a bit lower for big productions).That is the most common process to manufacture cold plate.
Pros: this is the most economical way to manufacture a cold plate for main cases. The pressure loss is low due to a good fluid flow through the cold plate. We can make CNC operation on the whole surface to prepare the component assembly on the cold plate.
Cons: the flatness on the machined side (the one with the tube) cannot reach really low level. A tool is required for tube forming.The side with the tube cannot be in contact with some material for example for food industry or medical application. However, there is no problem on the other side which is only one metallic material (aluminium for example).
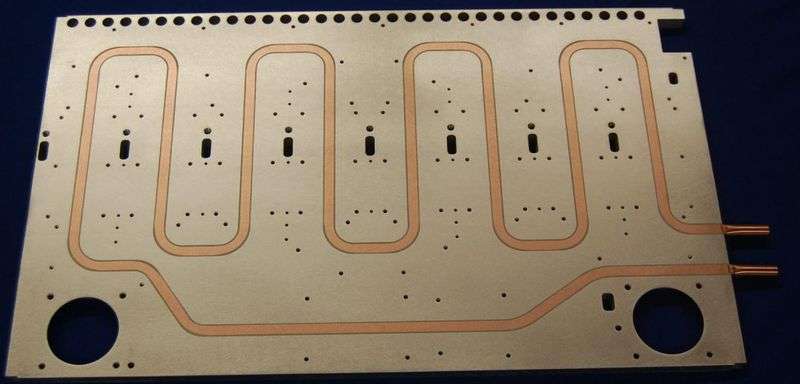
Drilling through a metallic plate (mainly aluminium).
The metal sheet is drilled to permit the fluid to circulate inside of the cold plate.
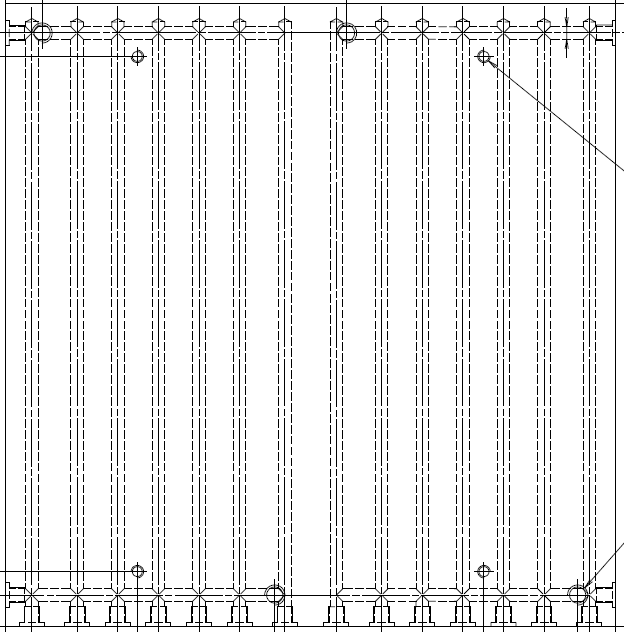
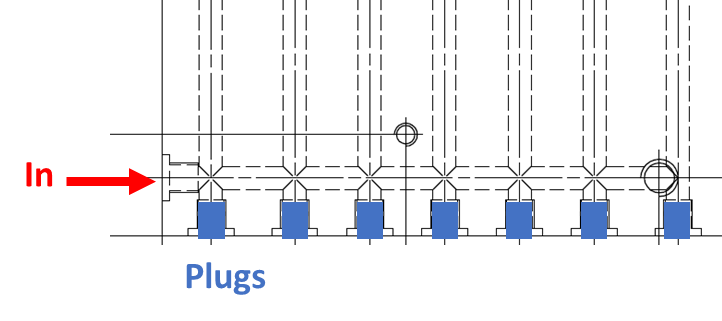
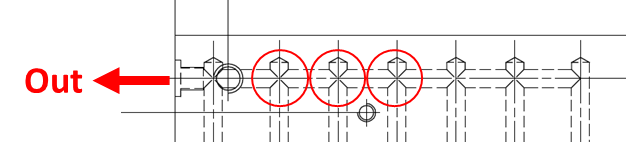
Pros: the manufacturing cost is low, because it is only drilling. There is no tooling required to manufacture this cold plate.
Cons: the plugs used to seal the openings of the tubes are expensive and can represent a consequent part of the part cost.
Cons: The drilling process makes “dead zones” in the cold plates:
These dead zones can be problematic on long term use because of residues stagnating in these zones. The pressure loss is also higher as the fluid circulation is less smooth in the cold plate.
Aluminium welding and Friction Stir Welding (FSW):
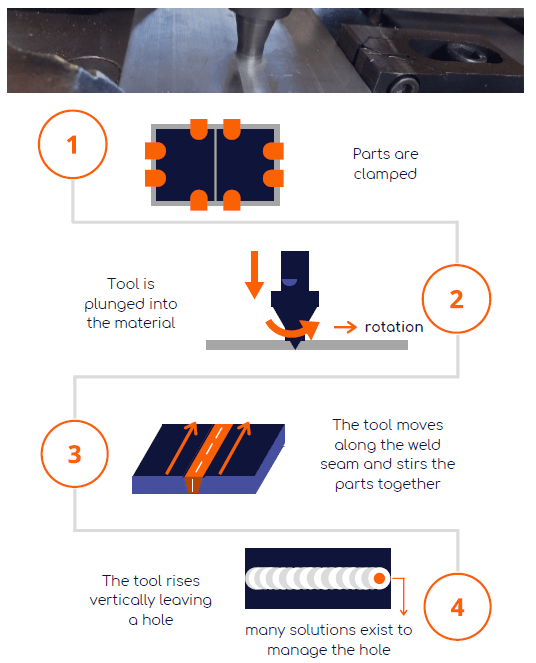
The Friction Stir Welding (FSW) process consists by soldering two aluminium parts without adding any material. The process melts the aluminium of the part to make the welding.
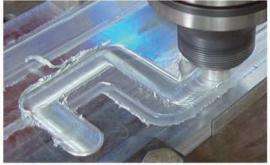
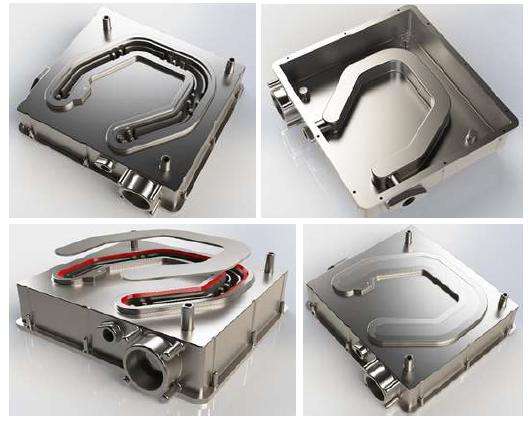
Pros: Lower production cost than screwing and sealing. Higher mechanical properties. Lighter, waterproof and excellent resistance to thermal shocks.
Cons: Depending on the design it might not be the most economical solution to manufacture a cold plate (comparing with tubes laminated on a machined cold plate). Dimensions is also limited. Maximum dimensions are 1 500*1 000mm and thickness 20mm.
What machines to manufacture a cold plate:
We use different machines in order to manufacture cold plates. Each one has its own specification and allows us to propose few prototypes to mass production.
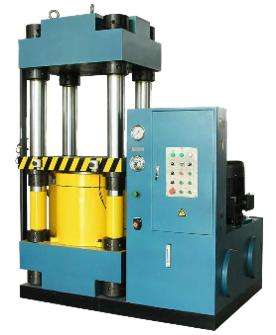
Stamping Machine: up to 500 tons pressure
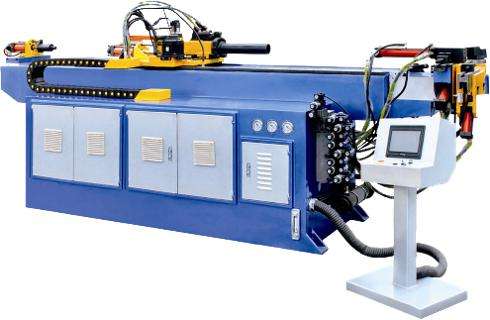
Tube Bending Machine for Cold Plate with Laminated Tubes
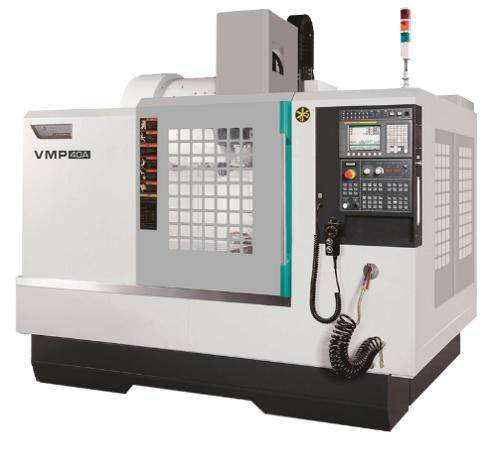
CNC Machine to prepare Cold Plate and Machine following Drawings
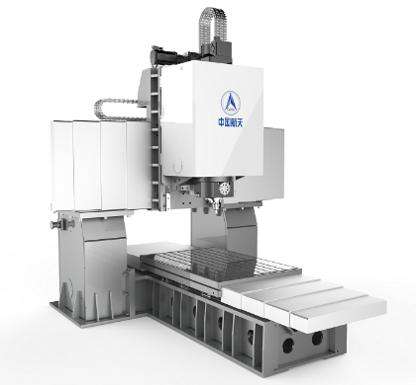
Friction Stir Welding (FSW) Machine for Aluminium Welding
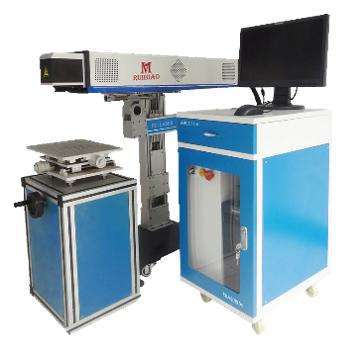
How are the cold plate controlled?
Every cold plate produced is controlled. Different tools exist to control and certify the quality of the process and of the product.
Ultrasonic tube thickness measuring
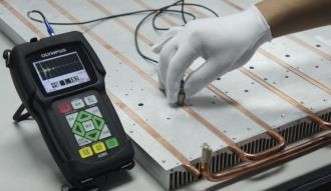
This tool measures the thickness of the tubes to be sure that there is no leakage risk.
Leaking Testing
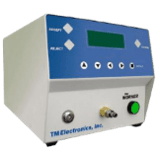
This tool controls the total sealing of the cold plate with different pressures.
Microscope Tube inspection
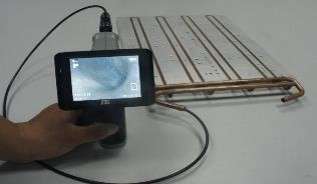
This tool is used to check the inner side of the tubes, and be sure that the flow inside the tubes will be smooth.
Flow and Thermal Testing
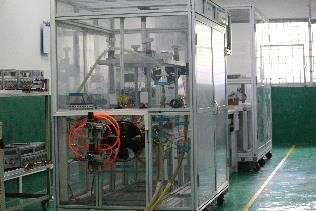
The cold plates are tested under different flow and temperature conditions to be sure that the mechanical comportment fit to the defined specifications.
Visual Inspection of the Tubes
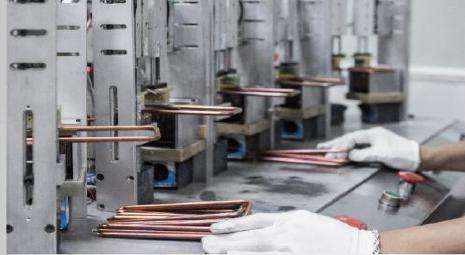
All materials and parts required for cold plates are strictly controlled before assembly.
What could go wrong with a cold plate?
Cold plates may have some weak points. Keep them in mind when integrating your own system.
Pump Reliability: All Electro-mechanical devices such as pumps have finite life which leads to reliability issues.
Fluid Permeation Loss: Fluids tend to permeate through polymer materials and joints. If too much fluid is lost due to permeation, the cold plate efficiency will drop and the system will stop working.
Fluid Leakage and Environmental Impact: Environmental concerns with cooling fluid leakage and disposal are issues.
How to resume cold plate?
Liquid cooling using cold plate is a necessary technology when power densities are too high to be managed by traditional air cooling. Indeed, liquid heat transport capabilities are far much greater than air.
The cold plate is integrated in a global thermal management system (pump, cold plate,heat exchanger, liquid line).
Cold plate is a relatively simple system, with a flexible design making it simple to integrate on different electronic projects wherever thermal performance above air cooling is required.
Different technologies and materials exist, and can be used to make the perfect thermal management system for your electronic project.
What about cold plate for your project?
Compelma team can help you to integrate cold plates for the thermal management of your electronic system. We can start from an existing design and make thermal simulation and mechanical suggestion.

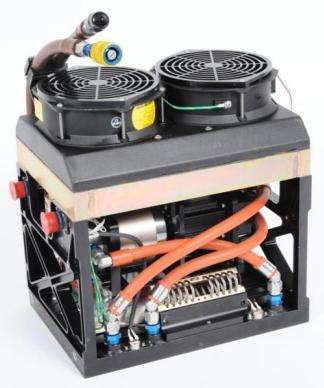
We have capacity to make prototypes (few units) to higher volume production at competitive prices.Our goal is to bring mechanical and design support (about materials and tolerances for example). We are always looking for the best ratio between efficiency, cost and quality on a controlled timeline.
We are use to work on different field of application, and so used to provide technical and quality documentation as FAI, CoC, Reach and RoHS certificates.
As Compelma is specialized on thermal management on electronic projects. We can also help you to increase the performance of your thermal management system by providing heat sinks and thermal interfaces for example. We can provide global thermal management system on request.